Cake Town
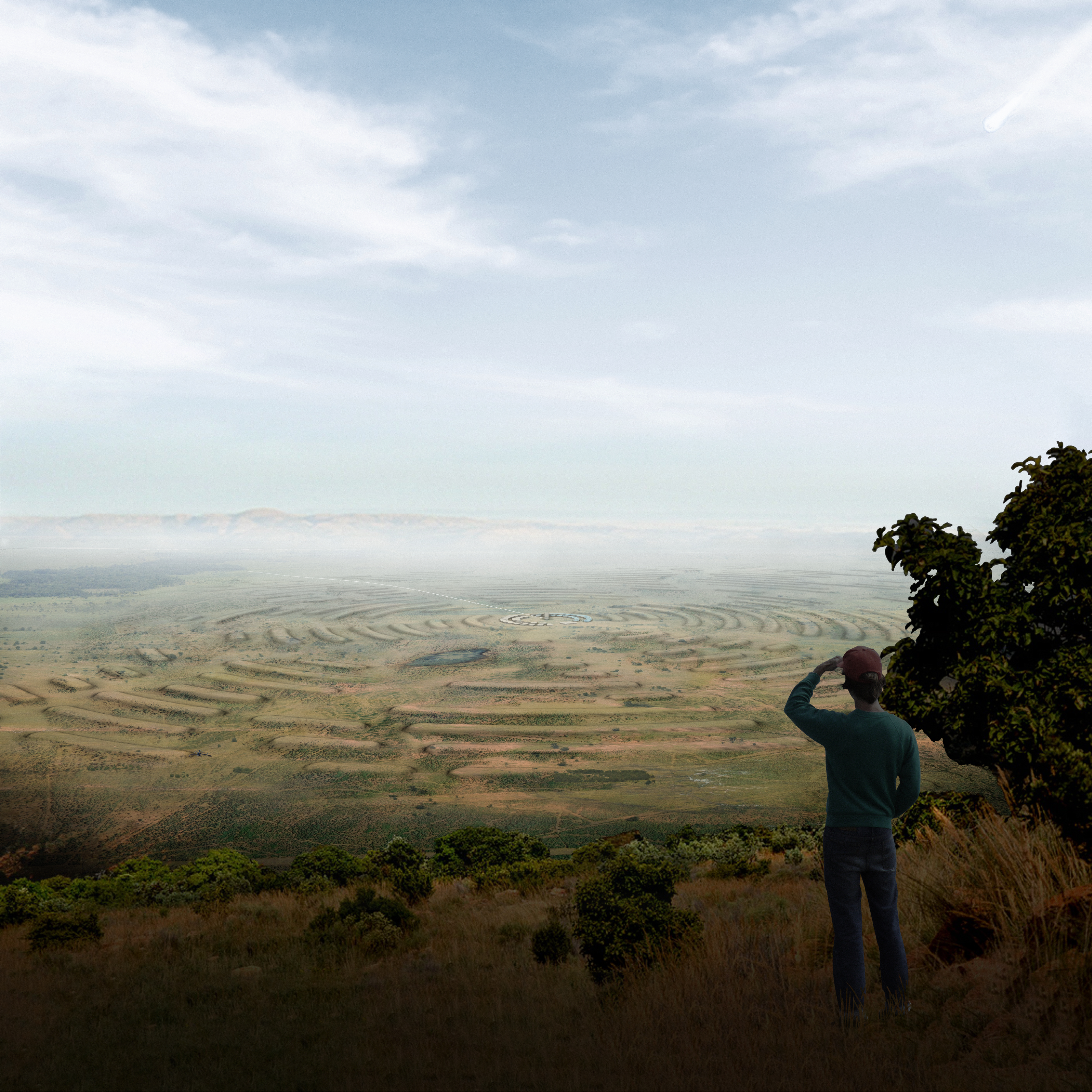
The meteor that struck South Africa 2,1 million years ago, fractured
the ground and angled the rock strata diagonally down into
earth, radiating towards the centre of the crater and ultimately
creating Witwatersrand. The gold-rich layers of the Witwatersrand
Supergroup were subsequently covered by layers of boulders and
dust, protecting it from erosion. This particular landscape condition
has led to the extraction of gold from 1886, resulting in hundreds
of tailings in the Gauteng region.
As seen in the mini-atlas ‘Off-cycle’, the tailing facilities
continue to have detrimental effects on the region and its people
through water, air, and ground pollution. However, re-mining
—which has become profitable due to the rise in gold prices—
provides a unique opportunity to reshape this landscape. The
project, situated in the centre of the Vredefort Crater, suggests a
final resting place for mine waste in which environmental effects
are controlled, spatializing the ungraspable impact of the mining
industry.
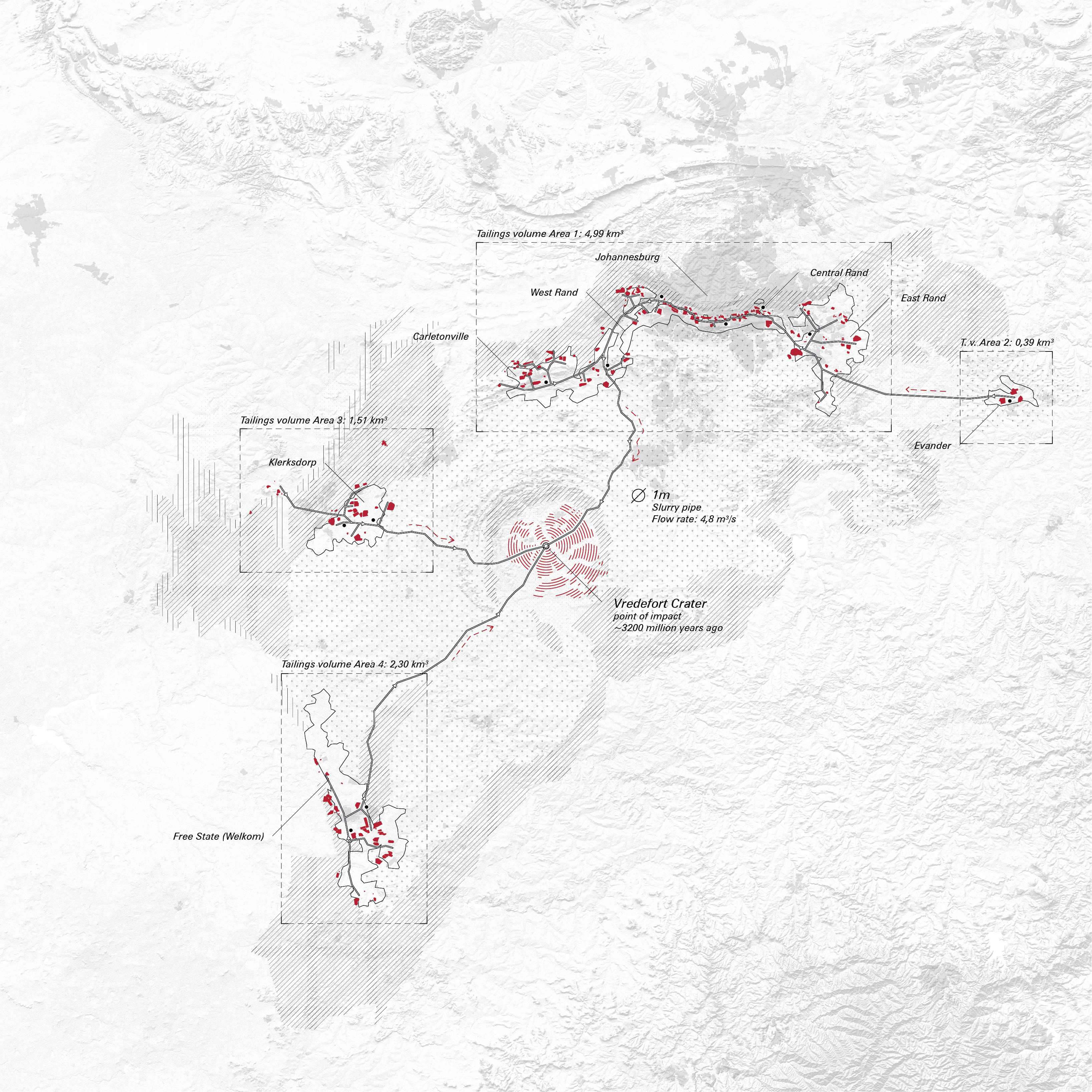
Reclamation & Deposition
Witwatersrand Basin
After the solid tailing material of the current deposition sites in the Witwatersrand is converted into slurry, it is filtered and re-processed by the existing processing plants to take out the remaining gold and uranium. The left-over slurry is then transported through pipes to the centralized tailing facility. At the facility, the material is converted into ‘cake’ by a process of dewatering. The now dry material is transported to the final deposition site, where it is stacked by so-called ‘spreaders’.

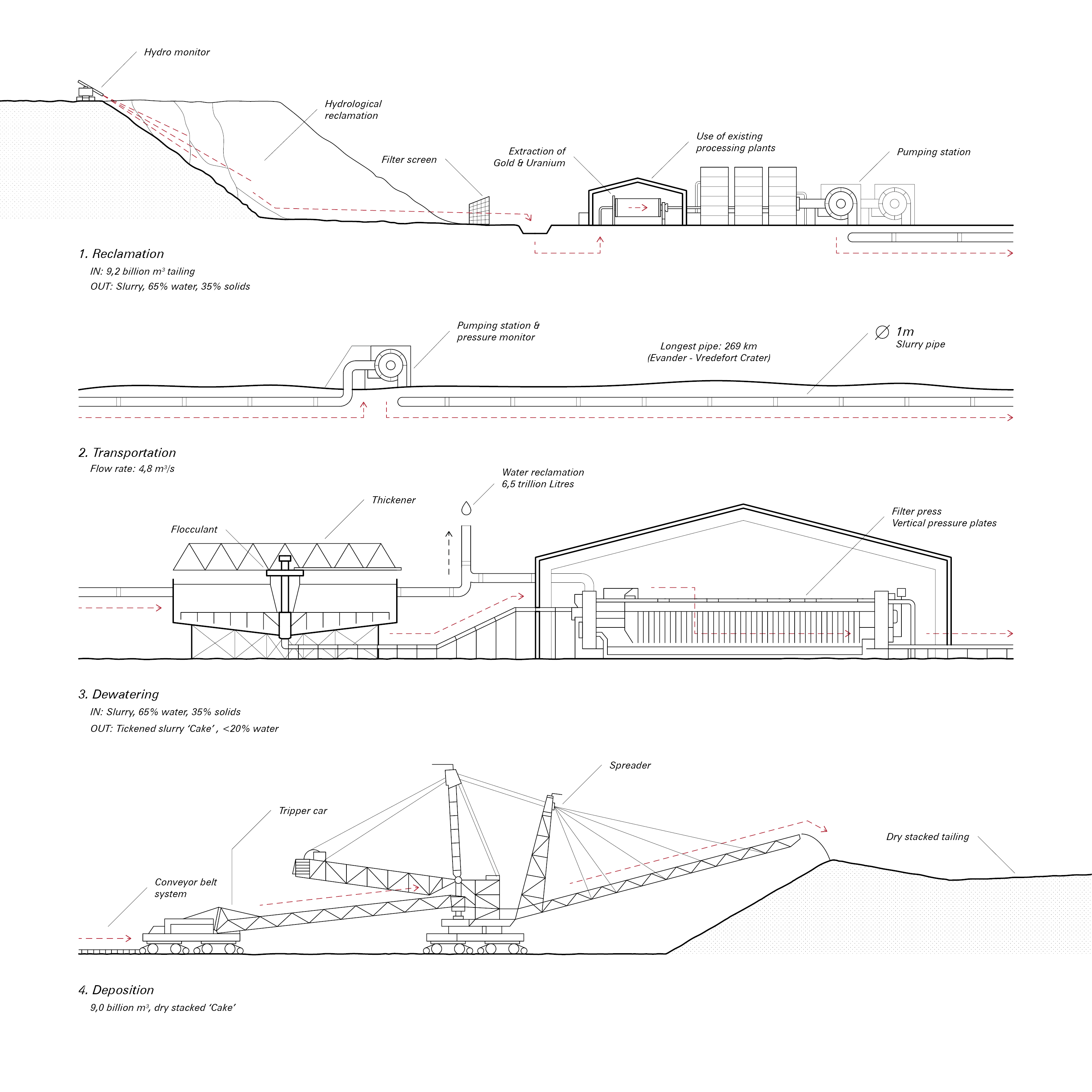
Process
Witwatersrand Basin
The solid tailing material is hydrologically reclaimed using water jets. The liquid substance called ‘slurry’ is filtered, collected and transported to local processing plants to take out the remaining gold and uranium. The left-over slurry is transported to the central tailing facility through underground pipes with a diameter of 1m, allowing for a flow rate of 4,8 m3 /s. In the central facility, a dewatering process that uses a Thickener and subsequently a Verticle Press transforms the ‘slurry’ into ‘cake’, a material that consists for less than 20% out of water. The cake is transported by conveyor belts to site of deposition, where it is stacked by a system of a tripper car and spreaders.
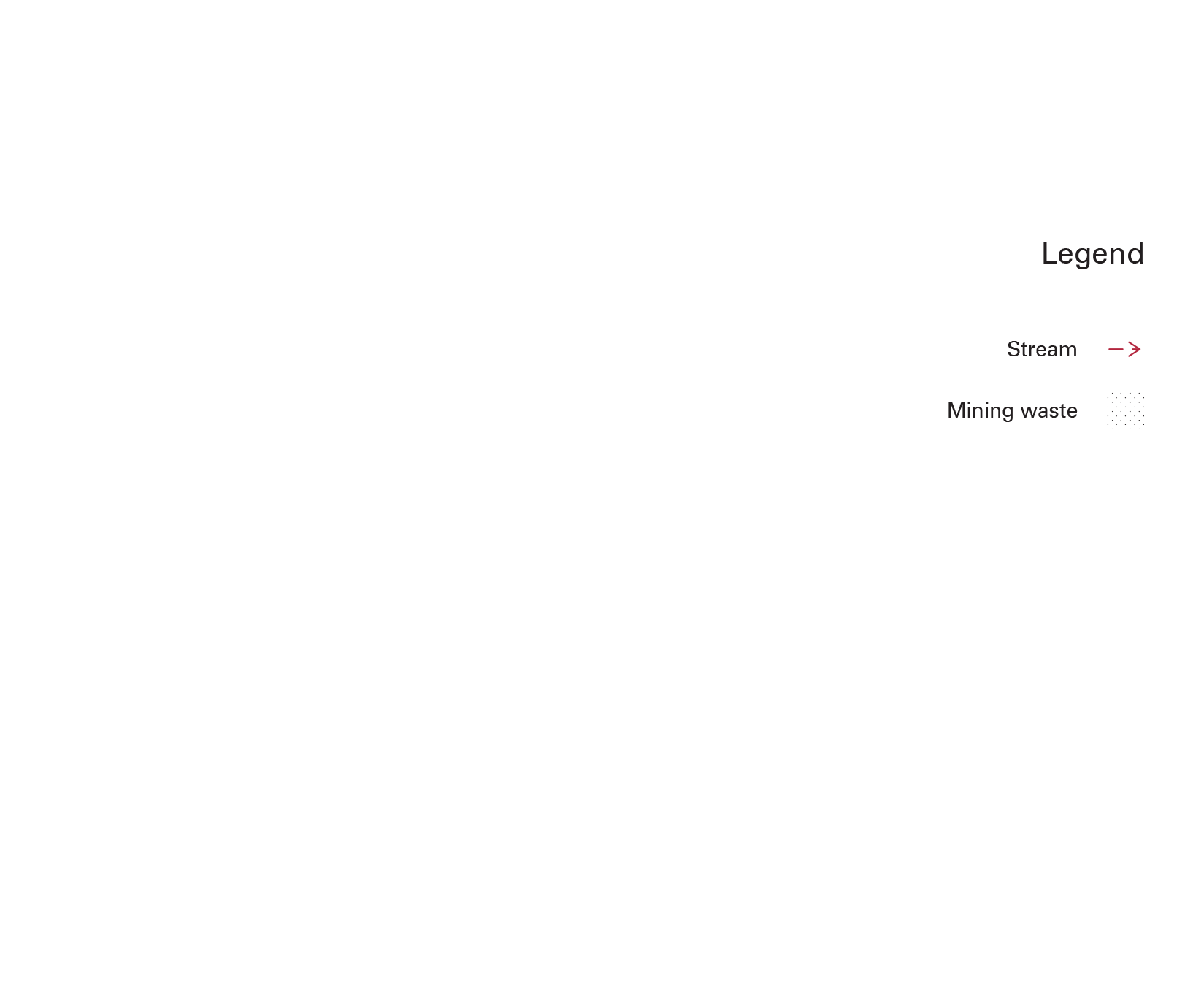